LED PCB Board Manufacturing
Aluminium LED PCB Board manufacturing
Aluminum PCB, or Aluminium PCB, also called Alu PCB, is one of Insulated Metal Substrate (IMS) PCBs, and is also one of the most commonly used Metal Core PCBs (MCPCB) nowadays. HitechPCB manufactures Aluminum printed circuit boards (PCB) with a full selection of high-performance substrates, and we work to be the best aluminum PCB manufacturer and provider no matter you need prototypes or high-volume production quantities. Aluminum PCBs typically are single-sided, but also can be double-sided as well. While, multilayer Aluminum PCBs are highly difficult to manufacture.
Thermal conductivity and thermal resistance of Aluminum LED PCB
As a widely used electronic component Aluminum LED PCB's thermal conductivity and thermal resistance are of great significance. The thermal conductivity of led Aluminum LED PCB is the quantity describing the conductor's ability to conduct heat, which can reflect the material's ability to conduct heat. Thermal resistance refers to the change rate of the temperature difference between the two surfaces during the heat conduction process of the surface of the object. In the design and application of electronic components, the thermal conductivity and thermal resistance of led Aluminum LED PCB play a decisive role.
Due to the different structure and composition of led Aluminum LED PCB, its thermal conductivity and thermal resistance will be different. Generally speaking, the greater the thermal conductivity of the led Aluminum LED PCB, the stronger the heat conductivity of the surface; And the smaller the thermal resistance, the smaller the temperature difference between the two surfaces. To sum up, the thermal conductivity and thermal resistance of led Aluminum LED PCB are very important parameters, which can affect the performance and service life of electronic components.
For different application requirements, the thermal conductivity and thermal resistance of led Aluminum LED PCB will be different. For example, in high temperature environments, Aluminum LED PCB with low thermal resistance and high thermal conductivity should be used; On the contrary, if it is in a low temperature environment, the Aluminum LED PCB with large thermal resistance and small thermal conductivity should be selected. Therefore, in the process of design and application, the thermal conductivity and thermal resistance of Aluminum LED PCB should be selected scientifically and reasonably according to the actual use environment and demand, so as to obtain better use effect. Hitech can provide a wide range of aluminum-based LED PCBS to suit customer requirements.
The relationship between insulating layer thickness and pressure resistance of Aluminum LED PCB
Aluminum LED PCB is a kind of basic material widely used in the field of electronics. The selection and thickness of insulating layer must be considered in the production process. Insulation layer is an important part of Aluminum LED PCB, its role is to prevent short circuit and leakage between different components on the circuit board, so as to ensure the normal operation of the entire circuit. The thickness of insulation layer is very important to the performance of Aluminum LED PCB and is closely related to the voltage it can withstand.
In general, the thicker the insulating layer of Aluminum LED PCB, the higher the voltage it can withstand. Because the thicker the insulation, the better you can isolate the different components on the board, reducing the possibility of short circuits and leakage. In addition, the thickness of the insulation layer can also affect the durability and stability of the Aluminum LED PCB, making it more durable and reliable.
However, too thick insulation can also bring unnecessary costs and manufacturing difficulties. Therefore, factors such as cost, reliability and performance must be considered comprehensively when selecting insulation layer thickness. Generally, the insulating layer thickness of Aluminum LED PCB should be between 5mil and 10mil, but can be adjusted for specific application requirements. For higher voltage requirements, a thicker insulation layer should be selected to ensure the stability and safety of the circuit board.
In summary, the insulating layer thickness of Aluminum LED PCB is closely related to its pressure resistance. Choosing the appropriate insulating layer thickness can improve the safety, stability and reliability of Aluminum LED PCB, so as to ensure the normal operation of the entire circuit. However, in the process of production, it is necessary to consider cost and performance factors to choose the most appropriate insulation layer thickness.
Thermal expansion of Aluminum LED PCB
Aluminum LED PCB is a unique metal substrate covered with copper substrate, it has good thermal conductivity, heat dissipation, electrical insulation and mechanical properties. Now let's talk about some properties of Aluminum LED PCB:
a. Thermal expansion of Aluminum LED PCB:
Thermal expansion and cold contraction is the common nature of substances, and the thermal expansion coefficient of different substances is different. Aluminum LED PCB can effectively solve the problem of heat dissipation, so as to alleviate the problem of thermal expansion and cold contraction of components on PCB board, and improve the durability and reliability of the whole machine and electronic equipment. In particular, the problem of hot expansion and cold contraction of SMT technology is solved.
b, heat dissipation:
At present, for many PCB boards with high density and power of double panels and multilayer boards, heat emission has become the most common difficulty. For example, FR4 and CEM3 are bad conductors of heat, interlayer insulation, and heat emission cannot go out. Local heating of electronic equipment cannot be excluded, leading to high temperature failure of electronic components. Thus it is widely used in high-power electronics, automobile electronic control, new energy savings, 5G communication products.
c, the ruler of Aluminum LED PCB is relatively stable, obviously the size is much more stable than that of the printed board of insulating materials. Aluminum LED PCB and aluminum sandwich board, from 30 degrees Celsius to 140~150 degrees Celsius C heating, the size change is 2.5~3.0%.
d, with shielding effect, instead of brittle ceramic substrate, safe use of surface mounting technology, reduce the real effective area of PCB board, replace the radiator and other components, improve the heat resistance and physical properties of the product; Reduce production costs and labor costs,
e. Structure: 1) a. aluminum base material, the use of LF, L4M, Ly12 aluminum, the expansion strength of 30kaf/mm2, elongation of 5%. Aluminum substrate is divided into 1.01.6, 2.0, 3.2mm 4 kinds, Aluminum models 6061T6 or 5052H34• Panasonic Electric, Sumitomo R-0710, R-0771, AL C-1401ALC-1370 and other models are aluminum base copper clad plate, the current thickness of aluminum base is 1.0~6.0mm. 2) insulation, usually 50~200um• If too thick, Can play the role of insulation, prevent and metal base short circuit effect is good, but will affect the heat dissipation if too thin, can be good heat dissipation, but easy to cause the metal core and component lead short circuit • Insulation layer (or semi-cured sheet), placed on the anodized, insulated aluminum plate, after laminating with the surface of the copper layer firmly combined together
Aluminum plate in the production of:
(1) aluminum oxide processing: strong oil cleaning (hydroxide) -- -- dilute acid neutralization, coarsening (aluminum plate surface to form honeycomb) -- -- oxidation (um) -- - alkali neutralization -- -- the bore is sealed by baking. Each process must ensure the quality or affect the adhesion of Aluminum LED PCB.
(2) The entire production process is not allowed to wipe the aluminum base surface, can not touch the aluminum base, damp and other dye, otherwise affect the Aluminum LED PCB bonding on it. Hitech in the production process strictly control each process, to provide customers with high quality Aluminum LED PCB.
Types of Aluminum LED PCB
Aluminum base plate commonly used metal aluminum base plate mainly 1000 series, 5000 series, 6000 series. The basic characteristics of these three series of aluminum are as follows:
(1) 1000 series on behalf of 1050, 1060, 1070, 1000 series aluminum plating, also known as pure aluminum plate. Of all series, Series 1000 contains the most is 2 layers of Aluminum LED PCB, purity can reach more than 99.00%. Because it does not contain other technical elements, the production process is relatively simple and the price is also relatively cheap. It is the most commonly used series in traditional industries. Most of the products in circulation are the 1050 and 1060 series.
The 1000 series aluminum plate is based on the last two digits to determine the minimum aluminum content of the series. For example, the last two digits of 1050 series are 50. According to the international brand naming principle, its aluminum content must reach 99.5% or more to be qualified. In the country's aluminum alloy technical standard (GB/T3880-2006), it is also clearly stipulated that the aluminum content of 1050 should reach 99.5%. Similarly, the 1060 series aluminum plate must contain more than 99.6 percent aluminum.
(2) 5000 series stands for 5052, 5005, 5083 and 5A05 series. 5000 series aluminum plate belongs to the more commonly used alloy aluminum plate series, the main element is magnesium, magnesium content between 3-5%, also known as aluminum magnesium alloy. It is characterized by low density, high tensile strength and high elongation. In the same area, the weight of aluminum magnesium alloy is lower than other series,
So it is often used in aviation, such as aircraft fuel tanks. In addition, it has a wide range of applications in traditional industries. Its processing technology is continuous casting and rolling, belonging to the hot rolled aluminum plate series, so it can be used for oxidation deep processing. In our country, 5000 series aluminum plate is one of more mature aluminum plate series.
(3) 6000 series represents 6061, mainly containing magnesium and silicon, so the advantages of 4000 series and 5000 series are concentrated. 6061 is a cold treatment aluminum forgings, suitable for corrosion resistance, oxidation resistance requirements of the occasion. It has good mach inability, excellent interface characteristics, easy coating, good processing performance.
General characteristics of 6061: excellent interface characteristics, easy coating, high strength, good workability, strong corrosion resistance. Typical uses of 6061 aluminum: aircraft parts, camera parts, couplers, Marine parts and hardware, electronic parts and connectors, etc.
Comprehensive consideration of the material itself texture, hardness, elongation, chemical properties, price and other factors, Aluminum LED PCB generally used 5000 series aluminum alloy 5052 aluminum plate.
Surface treatment technology of Aluminum LED PCB
After the electrical parts are inserted into the printed circuit board, they should be welded automatically. In these processes, if the material bubbling, in addition to the printed circuit board processing technology is not reasonable, but also related to the Aluminum LED PCB dip welding resistance. The poor impregnation and weld ability of Aluminum LED PCB will lead to the reduction of system quality stability and the damage of the whole components. Therefore, Aluminum LED PCB manufacturers attach great importance to the quality problem of impregnation and weld ability, which directly affects the product reputation of each manufacturer.
Aluminum LED PCB is a composite of resin, aluminum and copper foil curing. The thermal expansion coefficient of resin and aluminum, copper foil is very different, therefore, under the action of external force and heat, the internal force distribution of the plate is not uniform. If there are water molecules and some low molecules in the pores of the plate interface, under the condition of thermal shock, it will produce greater concentrated stress. If the adhesion can not resist these internal destructive forces, it will occur on the weak interface of copper foil and substrate, or lamination and foaming between the substrate layers.
To improve the weld resistance of Aluminum LED PCB, it is necessary to reduce the factors that will destroy the structure of various surfaces in the forming and high temperature of the plate. The improvement methods mainly include the surface treatment of copper foil and aluminum, the improvement of resin adhesive, and the control of pressure and temperature in the pressing process. Hitech circuits mainly on Aluminum LED PCB aluminum surface treatment to do some expressions.
Properties of aluminium substrates and surface treatment of materials
Aluminum LED PCB, is a kind of raw material, is a kind of metal base copper plate with good heat dissipation function. It is an electronic glass fiber cloth or other reinforcing materials soaked in resin, a single resin as insulating bonding layer, one or two sides covered with copper foil and made of hot pressing and made of a plate material, known as copper clad laminate Aluminum LED PCB, referred to as aluminum clad copper plate.
(1) Excellent heat dissipation performance
Aluminum clad copper foil plate has excellent heat dissipation performance, which is the most outstanding characteristic of this kind of plate. The PCB made from it can not only effectively prevent the working temperature rise of the components and substrate loaded on it, but also rapidly dissipate the heat generated by the power amplifier components, high-power components, large circuit power switches and other components. In addition, because of its low density and light weight (2.7g/cm³), it can prevent oxidation and has a low price. Therefore, it has become the most widely used composite plate. The saturated thermal resistance of the insulated Aluminum LED PCB is 1.10℃/W and 2.8℃/W, which greatly improves the fusing current of the copper wire.
(2) Improve the efficiency and quality of machining
Aluminum clad copper plate has high mechanical strength and toughness, which is much better than rigid resin clad copper plate and ceramic substrate. It can realize the manufacture of large area printed boards on metal substrates, especially suitable for mounting heavy components on such substrates. In addition, the Aluminum LED PCB also has good flatness, which can be used for hammering, riveting and other aspects of assembly processing on the substrate or bending and twisting along the non-wiring part of the PCB made of it, while the traditional resin copper clad plate can not.
(3) High stability of size
There is a problem of thermal expansion (dimensional stability) for all kinds of copper clad plates, especially the thermal expansion in the thickness direction of the plate (Z axis), so that the quality of metallized holes and lines is affected. The main reason is that the linear expansion coefficient of the plate is different, such as copper, and the linear expansion coefficient of epoxy glass fiber cloth substrate is 3. The linear expansion of the two is very different, easy to cause the thermal expansion of the substrate difference, resulting in copper wire and metallized hole fracture or damage. The linear expansion coefficient of the Aluminum LED PCB is between, it is much smaller than the general resin substrate, and more close to the copper linear expansion coefficient, which is conducive to ensure the quality and reliability of the printed circuit.
Advantages and disadvantages of Aluminum LED PCB are as follows:
● Meet the requirements of RoHs;
● More suitable for SMT process;
● In the circuit design of the thermal diffusion is very effective treatment, so as to reduce the module operating temperature, prolong the service life, improve the power density and reliability;
● Reduce the assembly of radiator and other hardware (including thermal interface materials), reduce product volume, reduce hardware and assembly costs;
● the power circuit and control circuit optimization combination;
● Replace fragile ceramic substrate, obtain better mechanical durability.
In which industries has Aluminum LED PCB been applied
First of all, Aluminum LED PCB is used more in audio equipment, especially audio amplifier, preamplifier, power amplifier and so on parts will be used in the production and processing process, will see that this substrate in the heat dissipation effect and insulation effect is more prominent, than traditional materials to be more safe and stable, This greatly reduces the safety risks in the process of installation or maintenance, and can stand out in all aspects of quality.
Secondly, the use of Aluminum LED PCB on the power supply equipment is more and more, when the regulator, regulator, converter and so on parts of the switch installation, its use characteristics are also very significant, in order to reach the first-class quality standards in the industry, so in the process of use to see the safety level of the equipment is constantly improving.
Again, the drive on the office automation equipment also began to add Aluminum LED PCB, because this in insulation and thermal conductivity coefficient standards have been further improved, see in the operation process to play out the technical performance is worthy of affirmation, for the operation is more and more safe. This is also the substrate in which the installation can achieve the effect and role, to achieve better performance.
Storage conditions of Aluminum LED PCB
Aluminum LED PCB are generally stored in a dark, dry environment. Most aluminum led PCBs are susceptible to moisture, yellowing and blackening. Generally, it should be used within 48 hours after opening the vacuum package.
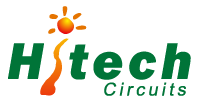
0086-755-29970700
sales@hitechpcb.com; sales@hitechcircuits.com
3F, B5 Dong, Zhimeihuizhi, FuYong, Bao’an Dist. Shenzhen, GuangDong, China 518103