Heavy Copper PCB Manufacturing up to 18 Oz
What is Heavy Copper PCB?
Heavy copper PCB is a circuit board with a copper thickness that is ≥ 3oz per sq. ft in its outer and inner layers. What makes a circuit board classified as a heavy copper PCB is its thicker plating. During the production of heavy copper PCB, copper thickness is enhanced through plated holes and sidewalls. For instance, when a PCB has 2 ounces of copper per sq. ft thickness, it is a standard PCB. However, if it has more than 3oz of copper, it is a heavy copper PCB. Heavy copper PCB is considered a reliable wiring option. Heavy copper PCB is different from extreme copper PCB which features within 20 oz to 200 oz per sq. ft.
What does Heavy Copper PCB offer?
Heavy copper PCB has a lot to offer. It has got some unique features that make it an ideal option for high-end applications. Let’s discuss some of the benefits of this PCB; Great thermal distribution: Due to its copper-plated vias, this PCB offers high thermal resistance. Heavy copper PCB are used in applications that demand high speed and high frequency. You can also use this PCB at harsh temperatures. Mechanical strength: Heavy copper PCB feature great mechanical strength. When this PCB is used, it makes the electrical system durable and robust. Good conductor: Heavy copper circuit boards are a good conductor. They are utilized in the production of electronics due to this feature. They help to link various boards together. These boards can transfer current.
How is Heavy Copper PCB Fabricated?
For the fabrication of heavy copper PCB, plating or etching is often used. The main aim is to add copper thickness to sidewalls and plated holes. The methods used in fabricating heavy copper PCB aren’t far-fetched. Heavy copper PCBs need special etching and plating methods to ensure the extra thickness of copper. Using the normal etching techniques for the fabrication of heavy copper PCBs isn’t ideal. Normal etching methods produce over-etched margins and edge lines that are uneven. PCB producers now use advanced etching and plating methods to achieve straight edges.
Heavy copper PCBs are produced via etching and plating methods. The major aim in the production of this PCB is to add copper thickness through sidewalls and plated-through holes. Heavy copper PCBs have several benefits which make them in high demand. Due to their outstanding features and benefits, they can meet your electrical requirements. These circuit boards will always dissipate heat generated due to heavy currents conduction. Electronics using heavy copper boards have been in use for a long time. Heavy copper can carry high currents. These boards will continue to meet the needs of various applications. High power circuit wirings can be developed using Heavy Copper PCBs. Such a wiring mechanism offers more reliable thermal stress handling and offers fine finishing while incorporating multiple channels on a single layer of a compact board.
Printed circuit boards (PCBs) are usually bonded with a layer of copper foil on a glass epoxy substrate. The thickness of the copper foil is usually 18μm, 35μm, 55μm, and 70μm. The most commonly used copper foil thickness is 35μm. Domestic copper foil thickness is generally 35 ~ 50μm, there are thinner than this such as 10μm, 18μm; And thicker than that like 70μm. The thickness of composite copper foil on 1~ 3mm thick substrate is about 35μm. The thickness of the composite copper foil on the substrate less than 1 mm thick is about 18μm, and the thickness of the cladding copper foil on the substrate thicker than 5mm is about 55μm. If the PCB copper foil thickness is 35μm, printed line width is 1mm, then every 10mm long, its resistance value is about 5mΩ, its inductance is about 4nH. When the di/dt of the digital integrated circuit chip on the PCB is 6mA/ns and the working current is 30mA, the noise voltage generated by each part of the circuit is estimated to be 0.15mV and 24mV according to the resistance value and inductance value of each 10mm printed line. Heavy Copper PCB boards can be made simply by combining two main processes: electroplating and etching. Compared to other PCBs, the circuit is made of a thin layer of copper foil. The copper plates are uniformly laminated with FR4 or other epoxy-based substances. The average weight of a Heavy Copper PCB can be 4 oz. (140μm), which is a better ratio than a copper-shared PCB. Let's look at the benefits.
Heavy Copper PCB Manufacturer & Circuit board Assembly – One-stop service Printed Circuit Boards (PCB) are usually coated with thick copper foil on a glass epoxy substrates commonly thickness of copper foil are 18μm, 35μm, 55μm, and 70μm. The most common copper foil is 35μm. The heavy copper PCB boards can simply be manufactured by two main processes plating and etching in the combine. As compared to other PCBs, the circuit is made of a thin layer of the Copper foil sheet. The plates of copper are laminated uniformly with FR4 or other epoxy-based substance. The average weight of the thick copper PCB weight could be 4oz (140μm), and this ratio is better as compared to another type of PCBs who have copper in common. Let’s check out the benefits of it.
Benefits of Heavy copper PCB Fabrication
Here are some of the advantages of heavy copper PCB, let’s follow them:
1. Favorable circumstances of Heavy Copper PCB
2. Plating innovation in overwhelming copper permitted a mix of plating and carving which causes in straight sidewalls and immaterial undercut.
3. The substantial copper plating creates high-current circuits and control circuits that watches the profoundly thick and straightforward whiskers’ structure.
4. This empowers the board fabricator to build the measure of copper thickness in plated gaps and by means of sidewalls.
5. The blend of substantial copper results on a solitary board called PowerLink.
6. The substantial copper in the PCB likewise encourages in associating with the standard circuits.
7. This lessens layer tally, low impedance control conveyance, littler impressions, and potential cost investment funds.
8. For development purposes, it expands the continuance to warm strains.
9. It has expanded the current conveying limit.
10. Overwhelming copper plating brings higher current through the board and moves the warmth to the outside heat sink
Application and advantage of Heavy Copper PCB in Electronic manufacturing
Heavy Copper PCB is a special PCB, its main characteristic is that the copper thickness is greater than or equal to 2oz. Compared with traditional PCB, Heavy Copper PCB has many advantages in electronic manufacturing. For example, they can withstand higher currents, have better heat dissipation capacity, better mechanical strength and better electrical properties. These characteristics make Heavy Copper PCBs widely used in high power equipment, such as electric vehicles, industrial robots, aerospace, mobile phones, microwave, satellite communications, network base station and other fields.
Take electric vehicle electronic control system as an example, electric vehicle electronic control system is one of the core components of the vehicle, has a very important role. In this kind of high-power electronic equipment, the range of current and voltage changes is very large, and the Heavy Copper PCB has better load capacity and heat dissipation capacity, which can ensure the stability and reliability of the electronic control system. Our customers use Heavy Copper PCBs in the production of electric vehicle electronic control systems to ensure the stability and reliability of the system under high power operating conditions.
When you decide to use a Heavy Copper PCB, you need to choose the right PCB manufacturer, Hitech Circuits will be able to offer copper plates in a variety of thicknesses and specifications to suit your needs. At the same time, you should ensure that your design meets the specifications and requirements of Heavy Copper PCB, including the wiring specifications of Heavy Copper PCB, welding pad specifications, etc. Finally, the right manufacturing process is also key, such as the selection of appropriate drilling, sheet laying and other processing steps to ensure quality.
In short, Heavy Copper PCB plays an irreplaceable role in the production and application of PCB industry, with high power, high current and high cooling effect. Heavy Copper PCB manufacturing process and materials have higher requirements than standard PCB. Hitech Circuits has advanced equipment and professional engineers to supply high quality Heavy Copper PCBs to domestic and international customers.
Heavy Copper circuit board technology introduction
(1) Preparation and plating treatment before plating
The main purpose of thickening copper plating is to ensure that there is enough Heavy Copper coating in the hole to ensure that the resistance value is within the range required by the process. As an insert is fixed position and ensure the connection strength; As surface-packaged devices, some holes only act as conduction holes, which conduct electricity on both sides.
Check item
a. Mainly check the metallization quality status of the hole, and ensure that there is no residue, burr, black hole, hole, etc.;
b. Check whether there is dirt or other residue on the surface of the substrate;
c. Check the number, drawing number, process document and process description of the substrate;
d. Make clear the installation and hanging position, installation and hanging requirements and the plating area that the plating tank can withstand;
e. Plating area and process parameters should be clear to ensure the stability and feasibility of plating process parameters;
f. Clean and prepare the conductive parts, and first energize the solution to make it appear active;
g. Determine whether the composition of the tank is qualified and the status of the surface area of the plate; If the cylindrical anode is used, the consumption must be checked;
h. Check the firmness of the contact parts and the fluctuation range of voltage and current.
(2) Quality control of thickened copper plating
a. Accurately calculate the plating area and refer to the effect of actual production process on current, correctly determine the required value of current, master the change of current in electroplating process, and ensure the stability of plating process parameters;
b. Before electroplating, the commissioning plate is used for test plating, so that the bath is in the activated state;
c. Determine the direction of the total current flow, and then determine the order of the hanging plate. In principle, it should be from far to near; Ensure the uniform distribution of current to any surface;
d. To ensure the uniformity of the coating and the consistency of the coating thickness in the hole, in addition to the technical measures of mixing and filtering, the impact current should be used;
e. Constantly monitor the change of current in the electroplating process to ensure the reliability and stability of current values;
f. Test whether the thickness of the copper plating layer in the hole meets the technical requirements.
(3) copper plating process
In the process of thickening copper plating, the process parameters must be monitored regularly, which often causes unnecessary losses due to subjective and objective reasons. To do a good job of thickening copper plating process, we must do the following aspects:
a. Add a certain value according to the area value calculated by the computer and the empirical constant accumulated in the actual production;
b. According to the calculated current value, in order to ensure the integrity of the coating in the hole, a certain value must be added to the original current value, namely, the impact current, and then return to the original value in a short time;
c. When the electroplating of the circuit board reaches 5 minutes, take out the substrate and observe whether the copper layer on the surface and the inner wall of the hole is complete, and the metal luster in all holes is preferable;
d. A certain distance must be kept between the substrate and the substrate;
e. When the thickened copper plating has reached the required plating time, a certain amount of current should be maintained during the removal of the substrate to ensure that no blackening or darkening will occur on the surface of the substrate or in the hole.
Note:
a. Check process documents, read process requirements and get familiar with lamina chart of substrate machining;
b. Check the surface of the substrate for scratches, indentation, copper exposure and other phenomena;
c. According to the mechanical processing floppy disk test processing, the first part of the pre-inspection, meet the technical requirements before all the workpiece processing;
d. Prepare measuring tools and other tools to be used for monitoring substrate geometry;
e. Select the appropriate milling tool (milling cutter) according to the raw material nature of the machining substrate.
Quality control
a. Strictly implement the first-part inspection system to ensure that the product size meets the design requirements;
b. Select milling processing parameters reasonably according to the raw materials of the circuit board;
c. When fixing the position of the circuit board, it should be carefully clamped to avoid damaging the solder layer and solder resistance layer on the surface of the circuit board;
d. To ensure the consistency of the overall dimension of the substrate, the position accuracy must be strictly controlled;
e. When disassembling and assembling, special attention should be paid to the layer of the substrate to pad the paper, so as to avoid damaging the plating layer on the circuit board surface.
The three characteristics of Heavy Copper PCB
1, bearing large current
When the line width is certain, increasing the copper thickness is equivalent to increasing the section area of the circuit, so the thickening of copper foil can make the circuit board carry more current.
2. Reduce thermal strain
Copper foil has a small conductivity (also known as resistivity, 1.72*10-8ΩΩ·m) through high current condition temperature rise is small, so it can reduce heat, thereby reducing thermal strain.
The conductivity is the resistivity. Metal "conductors" are divided into:
Silver → Copper → gold → aluminum → tungsten → nickel → iron.
3, Good heat dissipation
Copper foil has high thermal conductivity (thermal conductivity of 401W/mK), which can play an important role in improving heat dissipation performance, so it has good heat dissipation;
Thermal conductivity refers to the heat transferred through an area of 1m2 within 1H for a 1m thick material with a surface temperature difference of 1°C under stable heat transfer conditions. The unit is W/m·K.
Based on the above characteristics, it can be seen that Heavy Copper PCB is very suitable for high-current products. It has different characteristics and can better achieve circuit functions.
Application of Heavy Copper PCB
Heavy Copper PCBs have a number of benefits over standard PCBs. In addition, they offer excellent features that make them ideal for specific applications. For example, Heavy Copper PCBs are ideal for medical devices, and many other fields. As a result, the demand for Heavy Copper PCB is increasing.
Here are some applications of Heavy Copper PCBs:
Solar energy converter
Track traction system
Nuclear power industry
Automobile industry
UPS system
Protective relay
Torque control
Safety and signal system
Welding equipment
Power line motor
What can Heavy Copper PCBs provide?
Heavy Copper PCBs have a lot to offer. It has some unique features that make it ideal for high-end applications. Let's discuss some of the benefits of this PCB;
• Great heat distribution: This PCB provides high thermal resistance due to its copper-plated through-hole. Heavy Copper PCBs are used in applications requiring high speed and high frequency. You can also use this PCB in harsh temperatures.
• Mechanical strength: Heavy Copper PCBs have very high mechanical strength. When used, this PCB makes the electrical system durable and rugged.
• Good conductor: Heavy Copper circuit boards are good conductors. Because of this property, they are used in the production of electronic products. They help hold the various plates together. These plates can transmit electricity.
• Onboard radiators: Heavy Copper PCB provide onboard radiators. Using these plates, you can achieve an effective radiator on a Mosaic surface.
• Large dissipation coefficient: Heavy Copper PCBs are ideal for large components with high power consumption. These PCBs prevent the electrical system from overheating. They dissipate heat effectively.
Hitech Circuits is a professional PCB manufacturer with extensive experience in manufacturing Heavy Copper PCBs, as well as your other product requirements. We support sample and mass production, welcome to your inquiry.
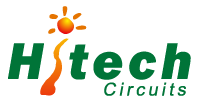
0086-755-29970700
sales@hitechpcb.com; sales@hitechcircuits.com
3F, B5 Dong, Zhimeihuizhi, FuYong, Bao’an Dist. Shenzhen, GuangDong, China 518103