Complete Guide on Ceramic PCB
Complete Guide on Ceramic PCB
What is Ceramic PCB?
Ceramic PCB board is also called ceramic substrate or ceramic circuit board, ceramic copper coated plate, ceramic substrate refers to the copper foil directly bonded to alumina (Al2O3) or aluminum nitride (AlN) ceramic substrate or other ceramic substrate surface (single or double) on the special process board. The ultrathin composite substrate has excellent electrical insulation performance, high thermal conductivity, excellent soft brazing and high adhesion strength, and can be etched into a variety of graphics like PCB board, with great current-carrying capacity. Therefore, Ceramic PCB board has become the basic material of high power electronic circuit structure technology and interconnection technology.
Ceramic PCB Manufacturing & Assembly – One-stop service The ceramic substrate (ceramic PCB) refers to a special process board in which a copper foil is directly bonded to a surface of an alumina (Al2O3 ) or aluminum nitride (AlN) ceramic substrate (single or double-sided) at a high temperature. The ultra-thin composite substrate produced has excellent electrical insulation properties, high thermal conductivity, excellent solderability, and high adhesion strength, and can etch various patterns like a PCB board, and has a large current carrying current ability.
What is Aluminum Nitride PCB (AlN PCB)?
Aluminum nitride (AlN) PCBs refer to a specific type of printed circuit board made using aluminum nitride (AlN) ceramic substrates as the insulating base material instead of the conventional laminated composites like FR-4.
In AlN PCBs, the aluminum nitride ceramic serves as the core dielectric layer that supports the conductive copper circuit layers. This is in contrast to standard PCBs that use fiberglass reinforced epoxy composites like FR-4 as the insulating substrate.
The conductive layers are typically deposited on the AlN ceramic surface through methods like screen printing, thin film deposition or direct bond copper (DBC). Holes can be formed in the AlN substrate to enable conductive vias between layers.
Compared to organic laminates, AlN ceramic provides superior thermal conductivity as an insulator while maintaining a close match to silicon’s coefficient of thermal expansion. This enables AlN PCBs to manage high temperatures and power levels without failure.
The relatively high cost of aluminum nitride ceramic material means AlN PCBs tend to be used selectively for demanding applications rather than as a wholesale replacement for conventional FR-4 boards. Common uses include power electronics, high brightness LEDs, and aerospace electronics.
In summary, Aluminum Nitride PCBs are a specific class of ceramic PCBs that leverage the unique benefits of aluminum nitride substrates for thermal management, temperature tolerance and reliability, especially in challenging operating environments.
Reasons why you should work with Ceramic PCB, especially for Aluminum Nitride PCB
Working with Aluminum Nitride (AlN) PCBs offers several compelling reasons, especially in applications where thermal management, high-frequency performance, and reliability are critical. Here are some key reasons to consider using Aluminum Nitride PCBs:
Exceptional Thermal Conductivity: AlN ceramics have excellent thermal conductivity properties, making them highly effective at dissipating heat generated by electronic components. This property is crucial for maintaining component reliability, extending the lifespan of electronics, and preventing overheating-related failures.
High-Frequency Performance: Aluminum Nitride PCBs: exhibit low signal loss and minimal signal distortion, making them well-suited for high-frequency and microwave applications. They provide reliable signal transmission and are ideal for RF (Radio Frequency) circuits, microwave antennas, and advanced communication systems.
Electrical Insulation: AlN ceramics possess excellent electrical insulation properties. They have a high dielectric strength, preventing electrical leakage and ensuring the isolation of electrical components and signals. This insulation is essential for maintaining signal integrity and preventing unintended electrical connections.
Mechanical Strength: AlN ceramic substrates have good mechanical strength, with the ability to withstand mechanical stresses during manufacturing, assembly, and operation. This mechanical robustness contributes to the overall reliability of electronic systems.
Compatibility with Semiconductor Devices: The thermal expansion coefficient of AlN is relatively close to that of silicon, a common material used in semiconductor devices. This compatibility allows for efficient heat transfer from semiconductor components, reducing the risk of thermal stress and enhancing their performance and longevity.
High-Power and High-Temperature Applications: Aluminum Nitride PCBs: are well-suited for high-power electronic components and high-temperature environments. They can efficiently dissipate heat from power amplifiers, voltage regulators, LEDs, and other heat-generating devices.
Longevity and Reliability: The superior thermal management provided by AlN PCBs contributes to the longevity and reliability of electronic systems, reducing the risk of premature component failures due to overheating.
Wide Range of Applications: Aluminum Nitride PCBs: find application in various industries, including aerospace and defense, telecommunications, medical devices, automotive, and industrial electronics. They are versatile and suitable for demanding electronic applications.
Customization: Aluminum Nitride PCBs: can be customized to meet specific design requirements, including layer count, dimensions, and design layout, ensuring that they are tailored to the needs of the application.
Efficient Heat Dissipation: The exceptional heat dissipation properties of AlN PCBs allow for the effective management of thermal issues without the need for additional cooling mechanisms, such as heat sinks or fans.
In summary, working with Aluminum Nitride (AlN) PCBs offers numerous advantages, including superior thermal conductivity, high-frequency performance, electrical insulation, and mechanical strength. These properties make them a preferred choice in applications where traditional PCB materials may not meet the stringent requirements for thermal management and reliability.
What are the Applications of Ceramic PCB?
Ceramic PCBs find applications in a wide range of industries and electronic systems where efficient thermal management, high-frequency performance, and reliable operation are essential. Here are some common applications of Ceramic PCBs:
High-Power Density Electronics (Converters and Inverters): Ceramic PCBs are vital in high-power density electronics like converters and inverters used in renewable energy systems, industrial machinery, and power distribution.
Electric Vehicle Power Systems and Charging Stations: Ceramic PCBs contribute to the thermal management and performance of electric vehicle power systems, including battery management systems and charging stations.
High-Intensity LED Systems: Ceramic PCBs help manage the heat generated by high-intensity LED systems, ensuring consistent and long-lasting illumination.
RF Amplifiers, Filters, Antennas: Ceramic PCBs are essential in RF applications, including amplifiers, filters, and antennas, where high-frequency performance and low signal loss are critical.
Space and Satellite Electronics: The extreme conditions of space and satellite environments benefit from Ceramic PCBs, which provide reliable thermal management and performance.
Downhole Drilling Tools: Ceramic PCBs are used in downhole drilling tools for the oil and gas industry, where they withstand high temperatures and harsh conditions.
Physics Research Instrumentation: Researchers use Ceramic PCBs in instrumentation for physics experiments due to their ability to maintain stability under varying conditions.
Medical Lasers and Thermal Therapy: Ceramic PCBs are employed in medical lasers and thermal therapy equipment, ensuring precise temperature control and performance.
High-Temperature Electronics and Sensors: Applications that require high-temperature electronics and sensors, such as industrial ovens and furnaces, benefit from Ceramic PCBs.
Nuclear Instrumentation and Radiation Detection: Ceramic PCBs are used in nuclear instrumentation and radiation detection devices, where reliability and thermal stability are crucial.
Automotive Radars and LiDAR: Ceramic PCBs play a role in automotive radar systems and LiDAR sensors for advanced driver-assistance systems (ADAS) and autonomous vehicles.
Aerospace Avionics: Aerospace avionics systems rely on Ceramic PCBs for their ability to withstand extreme conditions and maintain high-frequency performance.
Hybrid Microcircuits: Ceramic PCBs are used in hybrid microcircuits, which combine various technologies to achieve specific functionality.
These applications highlight the wide-ranging benefits of Aluminum Nitride PCB technology in industries ranging from electronics and telecommunications to energy, healthcare, and aerospace. Ceramic PCBs continue to drive innovation and improve the performance and reliability of advanced electronic systems.
Manufacturing Ceramic PCB
The fabrication process of Ceramic PCBs involves several essential steps, from substrate manufacturing to housing integration. These steps leverage the unique properties of Ceramic PCB such as its exceptional thermal conductivity, to create high-performance circuit boards. Here’s an overview of the general process:
1.Substrate Manufacturing
Ceramic PCB powder is formed into a billet through cold isostatic pressing (CIP). This process involves compressing the Ceramic PCB powder into a dense, cylindrical shape using hydraulic pressure.
Binder materials are added to the Ceramic PCB powder to facilitate the handling of the material during shaping and sintering.
The shaped billet is sintered at temperatures above 1800°C in a nitrogen atmosphere. Sintering fuses the Ceramic PCB powder particles together, creating a fully dense ceramic substrate with excellent thermal properties.
The Ceramic PCB board is precisely ground and polished down to the specified thickness, ensuring a smooth and uniform surface for subsequent processing.
Comparison of Aluminum Nitride PCB, Alumina PCB, and FR-4 PCB
When it comes to selecting the right material for printed circuit boards (PCBs) or other electronic applications, understanding the properties of each material is crucial. Aluminum Nitride, Alumina, and FR-4 are three commonly used materials, each with its own set of characteristics. Here’s a detailed comparison based on several parameters:
Parameter | Aluminum Nitride | Alumina | FR-4 |
Thermal Conductivity | 170-200 W/mK | 24-30 W/mK | 0.25-0.5 W/mK |
Dielectric Constant | 8.8 | 9.2-10 | 4.2-4.6 |
Dielectric Strength | 15-25 kV/mm | 10-15 kV/mm | 15-30 kV/mm |
Temperature Resistance | 1000-1500°C | 1000-1200°C | 130-170°C |
CTE (Coefficient of Thermal Expansion) | 4.0 ppm/K | 6.5-7 ppm/K | 17-20 ppm/K |
Flexural Strength | 330 MPa | 300 MPa | 180 MPa |
Analysis of Comparison:
• Thermal Conductivity: Aluminum Nitride PCB has significantly higher thermal conductivity compared to Alumina and FR-4, making it ideal for applications requiring excellent heat dissipation, such as high-performance electronics and LED lighting.
• Dielectric Constant: Aluminum Nitride PCB has a slightly lower dielectric constant than Alumina but higher than FR-4. A lower dielectric constant is generally favorable in high-frequency applications as it can reduce signal loss.
• Dielectric Strength: Aluminum Nitride PCB offers higher dielectric strength compared to Alumina, indicating better insulation properties under high voltage, but the range overlaps with FR-4.
• Temperature Resistance: Aluminum Nitride PCB withstands much higher temperatures compared to FR-4, and slightly higher than Alumina, making it suitable for high-temperature environments.
• Coefficient of Thermal Expansion (CTE): Aluminum Nitride PCB has a lower CTE compared to both Alumina and FR-4, implying less dimensional change with temperature fluctuations, which is critical for maintaining structural integrity in thermal cycling applications.
• Flexural Strength: Aluminum Nitride PCB is slightly stronger than Alumina and significantly stronger than FR-4, indicating that it can withstand higher mechanical stress, which is crucial in rugged applications.
Conclusion:
Aluminum Nitride PCB is superior in terms of thermal conductivity, temperature resistance, and mechanical strength, making it an excellent choice for high-power and high-temperature applications where traditional materials like FR-4 fall short. However, these enhanced properties come with a cost implication, and the choice between Aluminum Nitride PCB, Alumina PCB, and FR-4 will depend on the specific requirements of the application, including operational environments, electrical demands, mechanical stresses, and budget constraints.
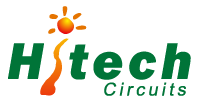
0086-755-29970700
sales@hitechpcb.com; sales@hitechcircuits.com
2F, Building C, Suojia Technology Park, Hangcheng, Bao’an, Shenzhen, Guangdong, China 518126